This year, in order to adapt to increased demand for our products, Termate invested in an additional high-performance injection moulding machine. We needed to take extensive consideration and planning for the installation of the new machine within our injection moulding manufacturing facility without disrupting the ongoing production.
Not only did we have to consider how the machine would fit into the floor space of our facility, but we also needed to consider; how it would arrive, how it would get to its intended position, how we would power the machine, and how we would change the tooling on the machine when in use.
This took an exceptional amount of forward-thinking as we would be increasing our number of injection moulding manufacturing machines from 3 to 4. We needed to ensure that our operators could work around the machine safely and the floor it was positioned on was structurally secure.
This new injection moulding machine will be critical in supporting us with one of our most significant projects to date. We began working closely with an international manufacturer in the energy storage market in May of last year. We became the sole supplier of specialised insulating bushings made specifically for this innovative energy storage system due to our capability to design, manufacture, and distribute low voltage insulating goods and parts. Our contribution to this next-generation energy storage technology will assure consistent output for many years to come.
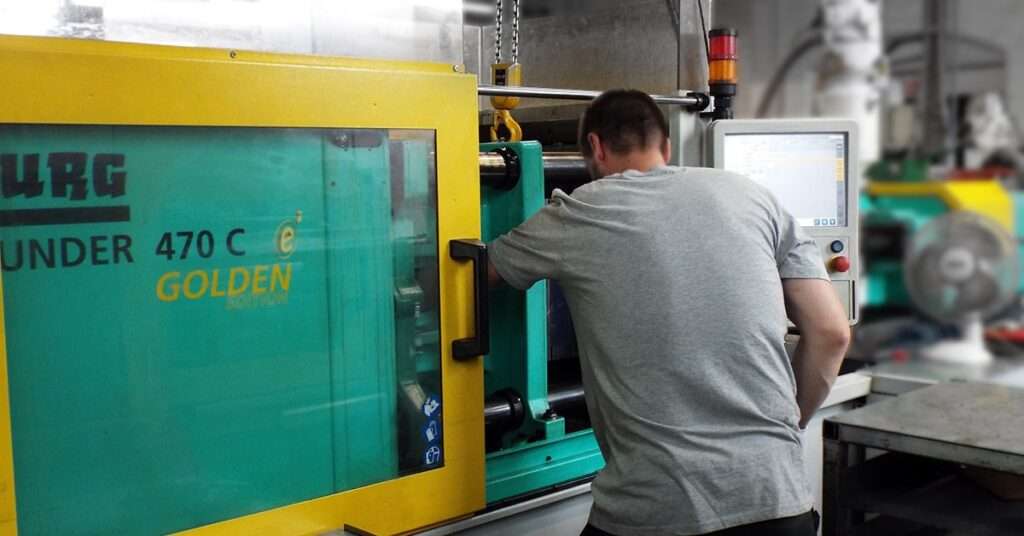
David Bristow, our Operations Director, explains how this acquisition will increase our production capacity for future work:
“Our new injection moulding machine continues our strategy of investment in modern energy-efficient equipment. All of our injection moulding machines have been replaced in the last 6 years in order to both maximise our production efficiency and reduce our energy consumption. The latest acquisition also extends our capability regarding larger component size and gives greater opportunity for proposing the most economic number of impressions within tooling, whether this be for our own products or those developed in-house for specific Customers.”
David Bristow, Operations Director
The opportunity to acquire a new machine for our manufacturing process has enabled us to produce both our standard products and in-house developed products for specific customers on a larger scale.
Discover Termate’s range of products and parts and you can contact us for your project’s specific requirements.